HLS12-30XXX | Download PDF |
HLS12-50XXX | Download PDF |
HLS12-100XXX | Download PDF |
Servos || Actuators
Specifications:
SG50BL-CAN-24V (Circular) | Download PDF |
SG33BL-T-12V/24V (DSUB) | Download PDF |
SG33BL-T-24V (Gland Cable) | Download PDF |
SG33BL-T-CAN-12V (Gland Cable) | Download PDF |
SG33BL-T-CAN-24V (Gland Cable) | Download PDF |
SG33BL-T-CAN-12V (Circular) | Download PDF |
SG33BL-T-CAN-24V (Circular) | Download PDF |
SG50BL-CAN-24V (Circular) | Download PDF |
SG33BL-T-12V/24V (DSUB) | Download PDF |
SG33BL-T-24V (Gland Cable) | Download PDF |
SG33BL-T-CAN-12V (Gland Cable) | Download PDF |
SG33BL-T-CAN-24V (Gland Cable) | Download PDF |
SG33BL-T-CAN-12V (Circular) | Download PDF |
SG33BL-T-CAN-24V (Circular) | Download PDF |
MD65MG-CAN/UAVCAN | Download PDF |
MD70MH-CAN/UAVCAN | Download PDF |
MD85MG | Download PDF |
MD85MG-CAN/UAVCAN | Download PDF |
MD89MW-CAN/UAVCAN | Download PDF |
MD145SW-CAN/UAVCAN | Download PDF |
MD245MW-CAN/UAVCAN | Download PDF |
MD250MW | Download PDF |
MD250MW-CAN/UAVCAN | Download PDF |
MD485MW | Download PDF |
MD950TW-CAN/UAVCAN | Download PDF |
MDB952SH-CAN/UAVCAN | Download PDF |
MD1100WP | Download PDF |
MDR845WP | Download PDF |
D485HW | Download PDF |
D646WP | Download PDF |
D951TW | Download PDF |
D954SW | Download PDF |
D980TW | Download PDF |
DB961WP | Download PDF |
HS-1005SGT | Download PDF |
HS-1100WP | Download PDF |
HS-53 | Download PDF |
HS-81 | Download PDF |
HS-85MG | Download PDF |
HS-311 | Download PDF |
HS-322-HD | Download PDF |
HS-325HB | Download PDF |
HS-645MG | Download PDF |
HS-646WP | Download PDF |
Analog servos/digital servos/linear actuators
From 1992, MULTIPLEX was the first manufacturer in the world to produce digital servos. MULTIPLEX has been part of the Hitec Group since 2002. Hitec is a leading servo and linear actuator manufacturer headquartered in Korea.
In addition to the highest demands in rc sports, Hitec servos also meet the required industry standards for a wide variety of automation and robotic applications, but also in the UAV/UAS, ROV and consumer sectors.
The Hitec product portfolio includes servos weighing less than 8g, but also real powerhouses with an actuating force of up to 50Nm. You need an actuator that works reliably in wet environments, some of our products are rated up to IP68.
As an affiliate company to Hitec RCD Korea Inc. we are able to fulfil requirements specific to particular clients. The following adaptations / modifications are possible:
- Changes to cable type and cable length
- Change to different connector
- Different selection of accessories
- Adaptation to packaging (external packaging, container size)
- Programming service
- Installation service
- Expanded goods output testing (test stand, logging)
- Changes to printed legends (nameplate, serial No., etc.)
- Product adaptation (e.g. gearbox reduction ratio)
- Fulfilment of particular certification requirements
- Component tracing
- Special delivery agreements (order framework, guaranteed delivery capacity)
Analogue actuators are generally low-priced to mid-priced items, and most of them are equipped with inexpensive components. The motor is always a D.C. brushed unit. Actuators offer no user-programmable options. Communication is always based on a PWM signal with a frequency of 50Hz. The motor PWM is the same as the control frequency, i.e. it is also 50Hz. This means that the possibility to control activity (motor on or motor off) only occurs every 20ms. Slow movements or small corrections result in long motor-off periods in relation to motor-on periods. The motor voltage is always the same as the power supply voltage.
Advantages:
• Reasonable price
• Pleasant running sound thanks to low motor frequency
• Low power consumption
Disadvantages:
• Low holding moment
• Slow response characteristics
• Low resolution due to low control frequency
• Wide deadband (20ms)
• Slow movements may not be smooth
Digital actuators generally fall in the high mid-range to high-price category. Very high-quality components may be used, such as Hall sensors for position sensing, as well as brushless D.C. motors. Communication is based on a PWM signal with frequencies up to 330Hz (according to actuator type) or other interfaces such as CAN, UAVCAN, RS-485 or TTL. The motor frequency is independent of the control system and is usually in the range 300 – 500Hz. This results in a very small possible deadband of up to 2ms. Digital actuators also offer wide-ranging programming and protective functions, as well as allowing two-way communication (feedback) depending on type.
Advantages:
• Fast response characteristics
• Fast corrective activity
• High holding power
• User-variable deadband
• Good accuracy
• Two-way communication
• Programmability
• Safety functions
• High resolution
Disadvantages:
• In most cases more expensive
• In some cases unpleasant running sound due to high motor frequency
• Higher power consumption
PWM communication
The conventional method of controlling Hitec actuators, with many advantages for simple tasks. Hitec PWM actuators can be controlled using a pulse width of 900 to 2100µs. The usual control frequencyis 50Hz (20ms), but frequencies up to 330Hz are possible with particular actuator types for special applications.
Actuators with PWM communication can easily be controlled at low cost, and they are adequate for many applications where feedback is not required.
The interface is in widespread use, and many controllers offer suitable presets and libraries.
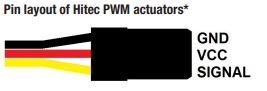
RS485 and TTL communication
There are a number of applications in several fields of operation for which feedback of the actual servo position is required, or at least desirable. Certain Hitec actuators are also available with RS485 and TTL interfaces, which enable them to work with two-way communication (feedback).
Hitec RS485 and TTL actuators communicate with external devices using the half-duplex process. TTL actuators of this type feature just one signal wire in addition to the voltage and earth conductors, whereas RS485 actuators feature two signal wires.

CAN and UAVCAN communication
The industrial and UAV field is becoming increasingly significant. This progressive, fast and technically highly complex market demands innovation and reliability. Many applications require intelligent solutions and genuine feedback of position, torque and other parameters in order to assess the application or to gain information about the condition of the components.
The following protocols are available: CAN 2.0A, CAN 2.0B, DRONE-CAN, UAVCAN
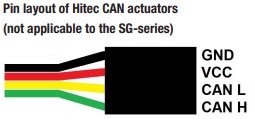
Mid-point and end-point adjustment (EPA / Neutral Settings)
Provides programmable mid-point and end-point servo positions.
Direction of rotation
Clockwise (CW) = when viewed from above, the servo output rotates clockwise when the signal width is increased.
Counter-Clockwise (CCW) = when viewed from above, the servo output rotates counter-clockwise when the signal width is increased.
Deadband (DB width)
The smaller the deadband, the sooner any corrective activity takes place when an angular change occurs. If the deadband is too low for the application, the result will be increased wear. Increasing the deadband results in loss of precision.
Travel speed
The servo’s transit speed: 100% equates to maximum possible travel speed.
ID-read / Node-ID
Assignment of an actuator ID in TTL and CAN networks.
Fail Safe
If the signal is lost, the servo rotates to a pre-selected position.
Fail Safe limp mode
The servo goes into sleep mode: the motor is disabled and the servo position is not maintained. The servo can be moved by hand.
Soft Start setting
When switched on, the servo runs to the nominal position at low speed in order to minimise stress on the gearbox and peripherals. At the 100% setting the servo runs to the nominal position with maximum transit speed when switched on.
Overload protection
Protection mechanism designed to avoid damage to the servo if it is overloaded or stalled. A setting of 20% corresponds to a reduction in maximum torque by 80%.
Smart sense
An intelligent regulatory circuit adjusts the control parameters while the servo is in use, in order to reduce oscillation. Oscillation can be
provoked by fluctuating inertia levels in the various applications. It is also possible to influence the regulatory circuit manually (sensitivity ratio settings). A high value may result in high-speed oscillation at the servo. A low value may generate severely damped response characteristics.
HLS-series (Linear Actuators)
Electrical linear actuators generating straight-line travel movements, making them suitable as replacements for pneumatic and hydraulic cylinders in many applications.
SG-series (Industrial Servos)
The premium industrial servo line, consistently developed for requirements in the fields of automation, unmanned aviation and robotics. Basic equipment includes a powerful BLDC motor, a Hall sensor for zero-contact, zero-wear position sensing, and watertight construction. All SG-series servos also feature a Multi-Turn* and Continuous-Rotation** function.
HSB-series (Brushless Servos)
Mid-priced servo motors with powerful BLDC motors.
HSR-series (Servos with Multi-Turn)
Mid-priced servo motors with Multi-Turn* and in some cases Continuous-Rotation** function. Most are equipped with a BLDC motor.
D-series (Digital Servos)
Mid-priced digital servo motors with a coreless or brushed motor. Fitted with a high-quality potentiometer for position sensing.
MD-series (Digital Servos with Magnetic Encoder)
Mid-priced digital servo motors with a coreless or brushed motor. Fitted with a Hall sensor for position sensing.
DB-series (Brushless Servos)
Mid-priced digital servo motors with powerful BLDC motors. Fitted with a high-quality potentiometer for position sensing.
MDB-series (Brushless Servos with Magnetic Encoder)
Mid-priced digital servo motors with powerful BLDC motors. Fitted with a Hall sensor for position sensing.
MDR-series (Digital Servos with Magnetic Encoder and Multi-Turn)
Mid-priced digital servo motors with Multi-Turn* and in some cases Continuous-Rotation** function. Fitted with a coreless or brushed motor. Fitted with a Hall sensor for position sensing.
HS-series (Hitec Servo)
Low-priced analogue servo motors, fitted with a brushed motor and a potentiometer for position sensing.
HS-1XXX, HS-5XXX, HS-7XXX series (Hitec Servo)
Mid-priced digital servo motors fitted with a coreless or brushed motor and a potentiometer for position sensing.
*: Several rotations are possible for maximum angular travel.
**: The servo is capable of continuous rotation.
Absolute position
The control system no longer has to rely on an actuator actually taking up the desired position; instead its current position can be read off with a resolution of 4096 steps.
Torque
Torque is a particularly important feature, as it allows the user to make assessments of the actual loads when the actuator is in use, as well as the condition of the components. Stiff mechanical systems can be detected and corrected in good time before they result in actuator overload. The torque value is derived from the motor PWM, and is therefore not an actual measurement, but it is adequately precise for the majority of applications.
Speed
How fast is the actuator when actually in use by the application? The actuator itself supplies the answer, thereby permitting important inferences to be drawn for many a control task.
Power supply voltage
The actuator constantly provides information on the momentary power supply voltage. The development or maintenance team can use this to detect potential weak points in the cable loom, for example: enabling high-resistance connectors to be replaced in good time.
Current drain
Current is the most important feedback element in preventing potential damage. Rising current over a given period of operation under a constant load is a reliable indication of an imminent fault. This may relate to the motor, the gearbox or the mechanical system being moved. Monitoring current drain opens up new possibilities in programming: effective system life can be extended by targeted optimisation of the internal control system (PID) and other parameters such as Soft Start (ramp) or deadband.
Micro-controller temperature
The temperature of the micro-controller is more than just a useful piece of information. Environmental conditions which include wide thermal variation can be very demanding on an actuator. Monitoring temperature in this way allows the development team to learn the thermal limits of the product, and to introduce appropriate measures to prevent premature failure.
Motor temperature
Are you asking too much of the actuator you are using? The motor temperature provides reliable information on whether an actuator is being operated close to its limit. This feedback is very important, especially if thermal conditions are widely variable.
Cycle counter
How many cycles does the actuator complete during use? How many parts were positioned? When must the actuator be replaced because the maximum cycle count has been reached? Some of our actuators supply this feedback in a convenient manner as part of the protocol.
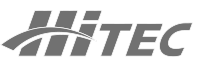
Although we can supply a large number of “standard servos / actuators” which are employed in many industrial applications and fulfil virtually all requirements, MULTIPLEX / HiTEC also offers the option of producing servos / actuators to your own specifications.
- Standard servos / actuators suitable for a wide range of industrial applications
- Customizing servos / actuators to suit your applications
- Programming of servos / actuators to your own specifications
Drones || Particle foam
ELAPOR® particle foam
MULTIPLEX was the first manufacturer to commence large-scale production of model aircraft moulded in particle foam, thereby ushering in the era of foam models. This technological innovation was developed in Germany, and for more than a decade has been the benchmark for outstanding quality; development continues constantly. Most MULTIPLEX model aircraft are manufactured in Germany.
UAV / UAS: This is another field in which ELAPOR® technology offers enormous advantages: the material is light in weight, extremely robust, impact-resistant, weatherproof, dimensionally stable, inexpensive and quick to repair. Moulded parts can be reproduced at low cost, even in large quantities.
We develop ELAPOR® products in-house, from start to finish, i.e. our own engineers and technicians supervise every project from the initial idea to the finished product. We can also provide the entire packaging process and even final assembly to complete our service.
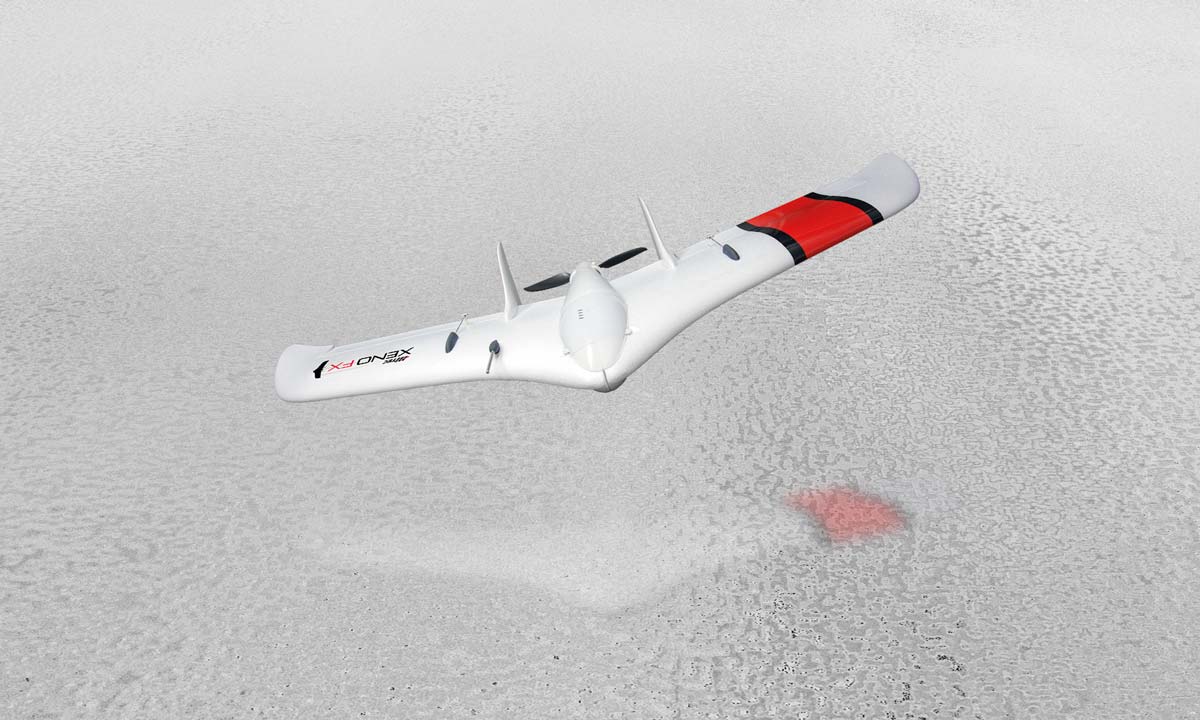
MARKEN: | ![]() |
PARTNER: | ![]() |
Remote control || UAV Controller
BeastTX
The next Generation All-in-One – the ultimate UAV Controller
PARTNER: | ![]() |
Brushless motors and speed controllers
We would be delighted to send you detailed specifications and drawings upon request.
Brushless motors and speed controllers
MULTIPLEX can supply a large selection of brushless motors and speed controllers. We can also produce custom-made articles to your specification upon request.
Brands: | ![]() |